Compressors
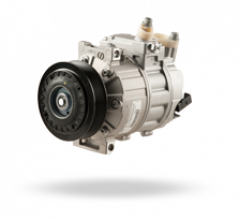
Valeo’s new compressors
The compressor is the driving element of the cold A/C loop and is also the most complex concerning technology features. Valeo, thanks to its expertise, offers a full range of new compressors with different technologies to meet a wide range of customer requirements.
A compressor is designed according to two main technologies: the piston type or the rotary type.
The piston type is the most common. This type contains swash plate technology and wobble plate technology. For the rotary type, vane and scroll technologies are used.
Valeo compressor technologies are identified under three names: DKV, DKS and DCS.
Each Valeo compressor is tested according to the OE process: leakage, durability, noise, vibration, etc.
With more than 440 part numbers, Valeo has the compressor you require. Thanks to its OE expertise and innovations in the technological features, Valeo meets car makers' requirements. Valeo compressors has an optimized design: a high quality finish and a precise selection of all components, especially for the valves, bearings, pistons, swash plates and clutches, guaranteeing high reliability and enhanced performance. Valeo strives to reduce noise and vibrations level for greater driver comfort.
Valeo Info: The compressor must be replaced after a crash, a breakdown or a leak. When replacing the compressor, a check and flush of the A/C loop and a change of the receiver drier and the expansion valve is necessary.
Valeo reman compressors
The compressor is among the most expansive component of the A/C loop while it is also the driving element. Valeo has thus developed a cost-effective solution to propose to your customer an alternative offer reman. The reman process is totally mastered by Valeo.
- The first step is to collect the cores and sort them according to their technical features.
- They are then disassembled, with the pump on one side, the clutch on the other side.
- All the parts are washed.
- The sub-components are remanufactured and controlled: more than 45 check points (visual, electric and functional) are done.
- All the wear parts are systematically replaced, and new components are used (O-rings, seals, bearing) to ensure durability.
- Finally, 100% of the production is tested: leak test, functional test, fill up with nitrogen to ensure stock safety.
Valeo is one of the best-in-class for remanufacturing process, based on O.E. process and specifications. This solution is at the same time cost efficient and environmentally friendly (+1kg Reman = -1kg CO2)